Sausage clipping, a critical component in the sausage manufacturing process, presents an intriguing landscape of innovation and efficiency for both new and seasoned producers. With technology advancements, selecting appropriate clipping systems becomes an essential factor in optimizing production lines and ensuring product quality—a priority for any business focused on maintaining authority and trustworthiness in the culinary industry.
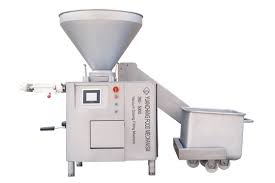
Understanding the intricacies of sausage clipping begins with recognizing its pivotal role in securing the ends of sausage casings once they are filled with meat mixtures. An expertly chosen clipping machine not only boosts production speed but also enhances the integrity of the sausage, preventing leaks and maintaining a uniform shape. However, selecting the perfect clipping system demands expertise and careful consideration of several critical factors.
First, it is vital to evaluate the production scale. Smaller-scale operations may choose manual clippers, which, although labor-intensive, provide a traditional touch and precision suitable for artisan batches. On the other hand, high-volume manufacturers lean towards automated clipping systems that significantly increase throughput without compromising on quality. Such systems offer customizable settings and quick-change clipping options that cater to different sausage types and casing materials, thus showcasing a noteworthy level of expertise in manufacturing flexibility.
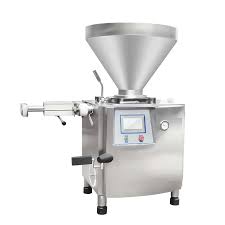
Another key consideration is the type of casing material being used. Natural casings, favored for their traditional taste and texture, require specific clipping pressures and mechanisms to avoid tearing. Artificial casings, including collagen and cellulose varieties, bring their own set of challenges requiring machines with adaptable settings. Experienced manufacturers acknowledge the importance of this adaptability to maintain product consistency and quality, reinforcing their credibility in the market.
sausage clipping
Durability and maintenance of clipping machines also reflect on a company's authority and reliability. Investing in equipment from trusted suppliers with a track record of resilience ensures minimal downtime and extended lifespan of the machinery. Regular maintenance schedules and the availability of spare parts should factor into purchasing decisions, as they directly affect production reliability and customer trust.
Safety standards in sausage manufacturing cannot be overstated. Ensuring that clipping machines comply with international safety regulations such as the EU Machinery Directive or the USA’s OSHA standards is non-negotiable. These guidelines not only protect employees but also assure customers of the manufacturer's commitment to safety and ethical production practices—a testament to the company's expertise and trustworthiness.
Furthermore, staying informed about the latest innovations in sausage clipping can provide competitive advantages. Emerging technologies like the integration of IoT devices in clipping machines present opportunities for real-time monitoring and data collection, optimizing performance and reducing waste. Companies embracing these advancements signal to their clientele a forward-thinking approach and a dedication to continuous improvement, thereby enhancing their authoritative stance within the industry.
In conclusion, a strategic approach to sausage clipping can profoundly impact production efficiency and product quality. By understanding the diverse needs of casing materials, selecting robust and compliant machines, and embracing cutting-edge technologies, manufacturers position themselves as authoritative and trustworthy leaders in the sausage production domain. Implementing these strategies will not only satisfy consumer demands for high-quality products but also fortify the company's reputation in the competitive culinary world.