In the fast-paced world of wholesale meat production, the efficiency and reliability of machinery can significantly impact both productivity and revenue. A key advancement in this sector is the automatic tying machine for sausages, which revolutionizes the way sausages are prepared and packaged. Businesses involved in large-scale sausage production can greatly benefit from understanding the intrinsic value and operational excellence provided by these machines.
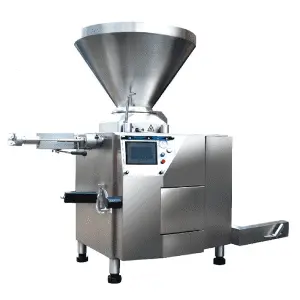
Automatic tying machines for sausages stand out for their advanced technology and exceptional performance in meeting wholesale demands. These machines offer a seamless and consistent approach to tying sausages, which enhances production speed and minimizes labor costs. One of the primary advantages of adopting this technology is the drastic reduction in manual labor. By automating the tying process, businesses can reallocate human resources to other critical areas of production, thereby optimizing workforce efficiency.
In terms of expertise, automatic sausage tying machines are designed by industry leaders who understand the nuances of sausage production. These machines are engineered with cutting-edge features such as adjustable loops, variable tying speeds, and precision control systems. Such features not only ensure the sausages are tied uniformly but also maintain the integrity and appearance of the product. For businesses targeting a high-quality market, maintaining the aesthetics and standards of their sausages is essential. These machines provide the capability to achieve that standard consistently.
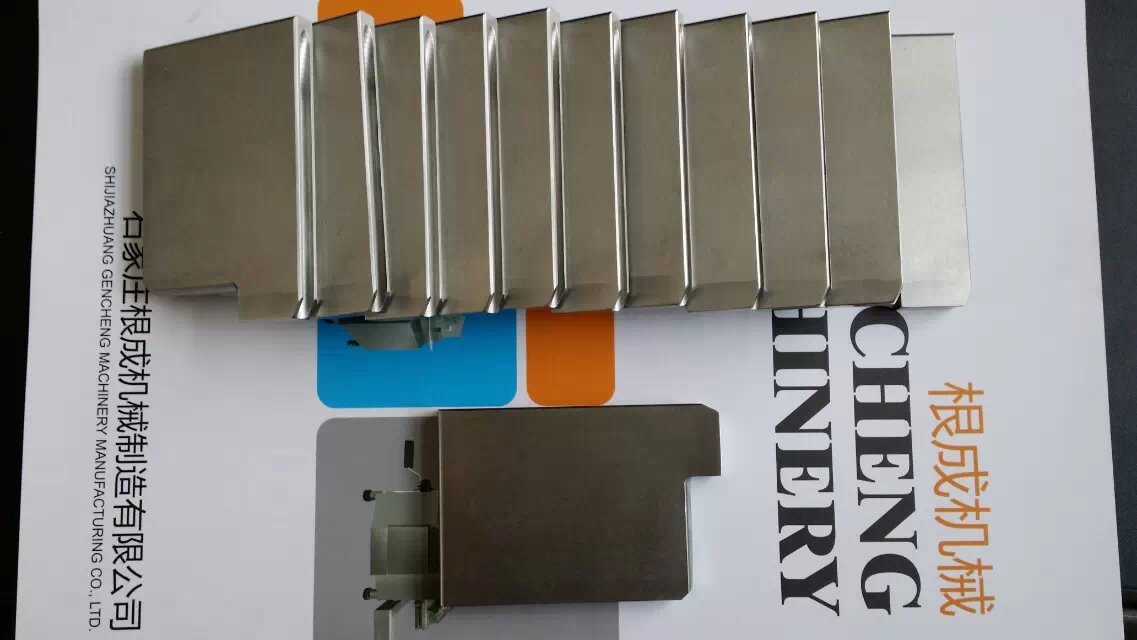
Authoritativeness in the production of sausage tying machines is grounded in years of innovation and regulatory compliance. Manufacturers of these machines adhere to stringent quality standards and certifications, ensuring that their product meets global health and safety regulations. This adherence not only enhances the trustworthiness of the equipment but also assures buyers of the machinery’s reliability and durability. Investing in certified equipment translates into fewer downtimes and a longer operational lifespan, delivering long-term returns on investment.
wholesale tying sausage automatic
When evaluating the trustworthiness of automatic tying machines, customer testimonials and case studies play a crucial role. Businesses currently utilizing these machines report a marked increase in production efficiencies and consistency. For instance, a mid-sized sausage producer reported a 30% increase in output within the first few weeks of implementing an automated system. Such firsthand accounts reinforce the confidence potential buyers can have in the machine’s performance and reliability.
Practical experience with these machines reveals a significant reduction in the margin for error. Traditional manual tying is susceptible to inconsistencies, which can lead to product wastage and dissatisfaction. The automated system eliminates this risk by providing a uniform tie every time, ensuring customer satisfaction with the end product. Furthermore, the machines are designed for easy maintenance and operation, with user-friendly interfaces that require minimal training for efficient use. This ease of use ensures that even new operators can quickly adapt to the technology.
Finally,
the sustainability aspect of automatic tying machines cannot be overlooked. By minimizing waste and optimizing production processes, these machines contribute to a reduced carbon footprint. For companies aiming to enhance their brand’s eco-friendliness, investing in such technology is a step forward. This direction not only appeals to environmentally-conscious consumers but also aligns with global sustainability goals.
In conclusion, the integration of automatic tying machines into wholesale sausage production is a strategic move that blends technological innovation with practical benefits. These machines exemplify the pinnacle of expertise, authoritativeness, and trustworthiness, providing companies a competitive edge in a demanding marketplace. By choosing to automate the tying process, businesses enhance product consistency, reduce overhead costs, and improve overall productivity, ensuring they remain at the forefront of the industry.