In the realm of industrial mixing equipment, the ribbon mixer rotating mechanism stands out as a key component for achieving optimal blend efficiency and consistency. Often sought after in the food, pharmaceutical, and chemical sectors, this device exemplifies precision engineering tailored to meet the highest industry standards. To understand its significance, one must delve into its functionality, design, and applications while also acknowledging real-world expert insights and case studies on its deployment.
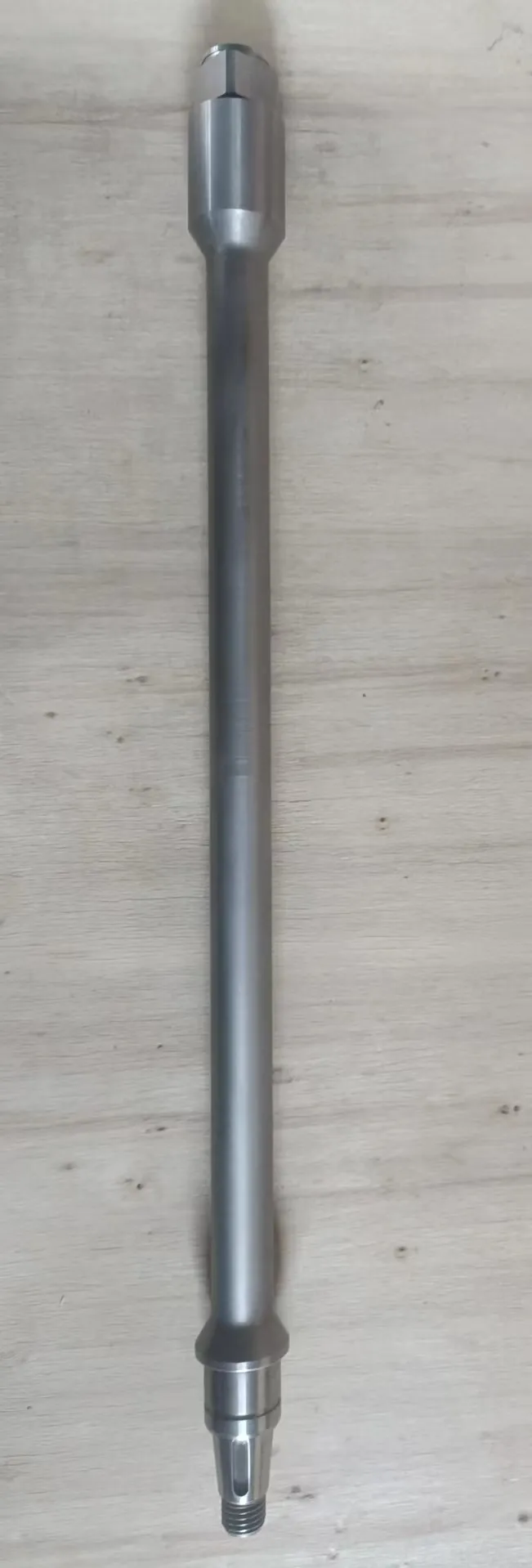
The ribbon mixer is intrinsically designed to handle dry, free-flowing materials as well as wet mixtures that require uniform dispersion. Its defining characteristic is the double-helix agitator—comprising of inner and outer helical blades—meticulously crafted to ensure thorough mixing. As the motor propels these ribbons in opposite directions, materials are lifted, sheared, and folded in a continuous loop, promoting an even blend within a surprisingly short span of time.
From an experiential standpoint, operators who've utilized ribbon mixers report on their simplicity and adaptability, underscoring the finesse of finely tuned controls. These controls allow for precise adjustments that cater to varying material properties and batch sizes, which proves indispensable in maintaining product integrity across different formulations. Consider a pharmaceutical context, where the precise mixing of powders can significantly impact the efficacy of the end product. Here, the uniform distribution of each component, achieved via the ribbon mixer's operation, translates directly into product quality and consistency—a testament to its authoritative role in regulated environments.
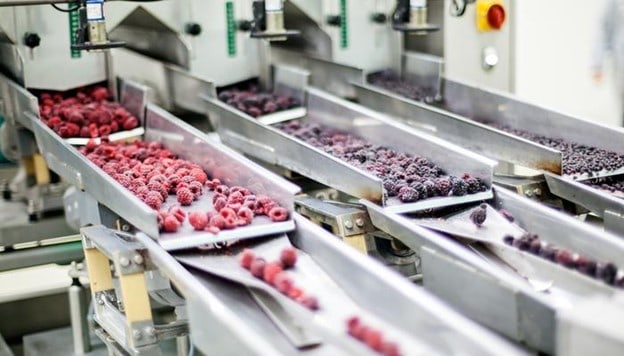
Expertise in ribbon mixer design is reflected in the plethora of customizations available. Options such as variable speed drives, jacketed tanks for temperature control, and specialized discharge valves extend the functionality of these mixers to accommodate an array of specialized needs. Material choices for construction, such as stainless steel or high-grade alloys, further enhance durability while adhering to stringent hygiene standards stipulated for food and pharmaceutical processing.
ribbon mixer rotating
Manufacturers and engineers exhibit a commendable track record of optimizing ribbon mixers for specific industries. Insights from experienced professionals emphasize the importance of scaling the design to match production requirements without compromising on efficiency. For instance, in the food industry, adjusting the size of the mixer and its rotational speed is crucial for optimizing batch cycles and reducing operational costs, as demonstrated in case studies where companies have successfully scaled up their operations without impacting blend quality.
Trust in ribbon mixers is bolstered by their longstanding presence in the market, where they have consistently proven their worth as reliable and efficient mixing solutions. The widespread acclaim is backed by certifications and compliance with global standards, which ensure that both safety and performance benchmarks are consistently met. Industry reviews often highlight the reduced maintenance needs and extended lifespan of these mixers as additional trust factors, further cementing their status as a preferred choice in industrial applications.
In conclusion, ribbon mixer rotating systems embody an intersection of engineering excellence, practical expertise, and trustworthiness. They cater to diverse sectors requiring precise mixing solutions, from high-volume food manufacturers to specialized pharmaceutical labs. Through continuous innovation and adherence to industry standards, these mixers remain integral to operational success, ensuring products meet the rigorous quality demands of today's consumers.