The realm of vacuum fillers, especially the rotor component, demands attention from seasoned professionals in processing and manufacturing industries. Their effectiveness and efficiency in filling applications are extraordinary, making them indispensable across several sectors.
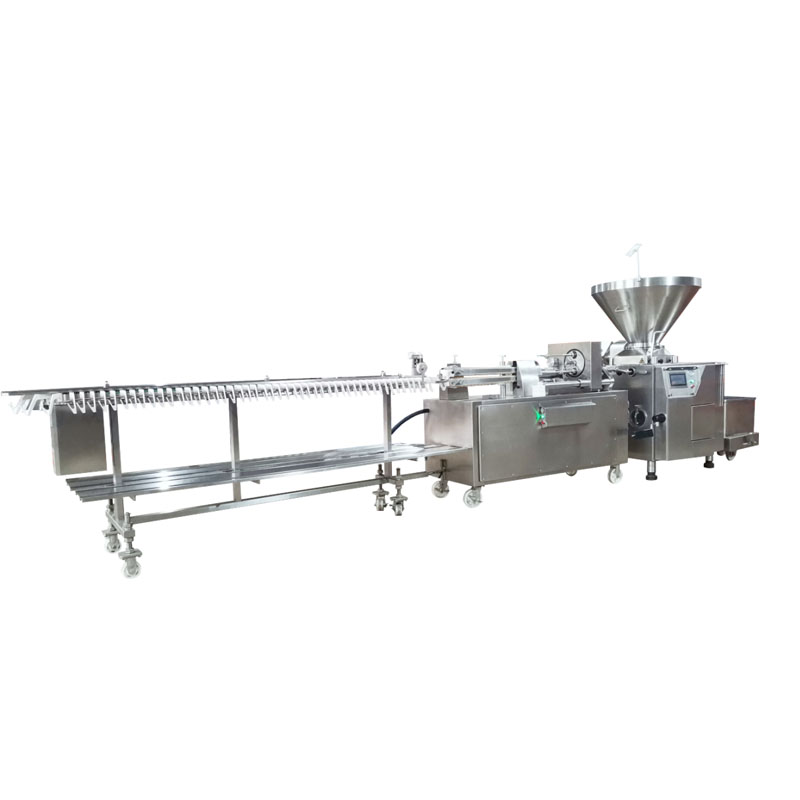
A rotor for a vacuum filler is an instrument of precision that channels product materials into the filler chamber, ensuring consistent dosing. According to industry experts, selecting the right rotor can profoundly impact the quality of the end product. This is particularly crucial in industries like pharmaceuticals, food and beverage, and cosmetics, where consistency is paramount.
Expertise in this domain suggests that the rotor's design is essential for the hygiene and reliability of the vacuum filler. It's often constructed from stainless steel or high-grade alloy, providing resistance against corrosion and ensuring longevity. Industry leaders recommend maintaining an ultra-clean surface finish of the rotor, as it directly contacts the substance being filled, mitigating contamination risks.
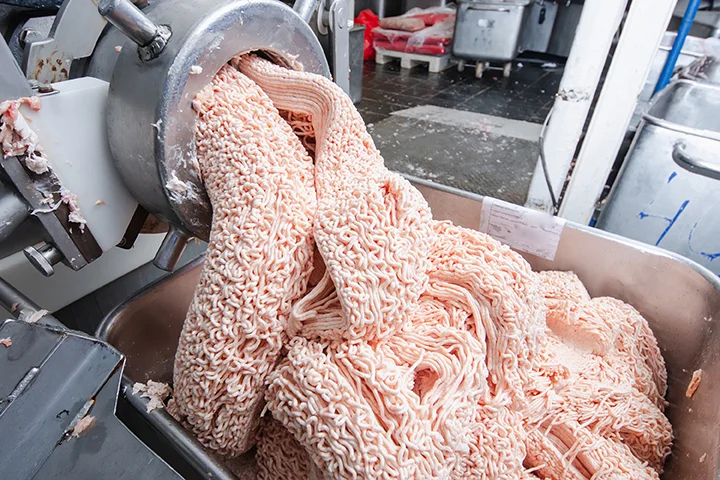
A rotor's efficiency is evident in its ability to maintain optimal speed and accuracy. This is achievable through engineering precision, which manufacturers strive to perfect. Recent innovations in rotor design have led to improvements in flow dynamics, minimizing residue and waste product — a pivotal advancement that appeals to eco-conscious operations globally.
Users with hands-on experience often highlight the importance of regular maintenance for rotors within vacuum fillers. Routine checks and maintenance schedules can prevent wear and tear, preserving the rotor's functionality. As noted by experienced technicians, even slight abrasions or deformations can affect the machine's performance, reinforcing the necessity for a robust inspection regimen.
In the pursuit of excellence, some manufacturers have adopted advanced technologies such as computer-aided design (CAD) and finite element analysis (FEA) simulations. These technologies aid in predicting wear patterns and optimizing the rotor's design before production commences, ensuring that any potential issues are identified and addressed at the prototyping stage.
rotor for vacuum filler
Trustworthiness in production processes involving vacuum fillers is non-negotiable. Producers emphasize the significance of choosing rotors tested and certified by reputable bodies, adhering to standards like ISO and GMP. Certifications offer a seal of quality that not only meets regulatory requirements but also assures end-users of the product’s safety and reliability.
When considering the purchase or replacement of a rotor, industry professionals recommend consulting with experts who have a proven track record. It's a step that can prevent costly downtimes and enhance performance. By focusing on detailed specifications such as rotor diameter, chamber compatibility, and material properties, businesses can ensure they are investing in equipment that aligns with their operational demands.
Exploring the latest trends, the industry is witnessing an increased interest in customizable rotors. This customization allows rotors to be tailored to specific operational needs, balancing flexibility with standardization. By embracing modular designs, companies are crafting unique solutions that cater to the varying viscosities and temperatures of materials.
Rotor manufacturers are increasingly prioritizing sustainability in their production methods. The use of sustainable materials and practices not only aligns with contemporary environmental agendas but also reduces manufacturing costs, a benefit passed down to clients. A shift towards greener practices demonstrates a commitment to corporate social responsibility while still meeting essential operational benchmarks.
In summary, the rotor for a vacuum filler is more than a mechanical component; it's a critical player in ensuring precision, hygiene, and efficiency. Organizations that recognize the rotor's pivotal role in the vacuum filling process are adept at harnessing its potential, ultimately leading to superior product quality and market leadership.